Underwater inspections
Elevate Your Inspection Capabilities with Water Linked.
See Product Options Contact us
Our products are designed to support a wide range of underwater inspection needs, including inspections for pipelines, powerlines, general infrastructure, and (nuclear) power plants. Choose Water Linked for your underwater inspection technology needs and experience the advantages of integrating our advanced technology for increased levels of precision, safety, and operational excellence.
Increase navigation precision and control
of your underwater vehicles
A DVL is used to calculate the velocity of your underwater vehicle. When fully integrated with a control system this data is used to increase the navigation capabilities of underwater vehicles. Our DVL A50 and A125 have a built-in IMU that will let you attain dead-reckoning navigation for short missions without drifting. For medium-long inspection missions, we recommend integrating our DVL with an INS.
Our DVLs don’t just help ROVs and AUVs with navigation. When integrated well with other sensors in an ROV or AUV, our DVLs can also:
- Increase the vehicles' control and stability
- Allow vehicles to hold position (station keeping)
- Help with automated navigation
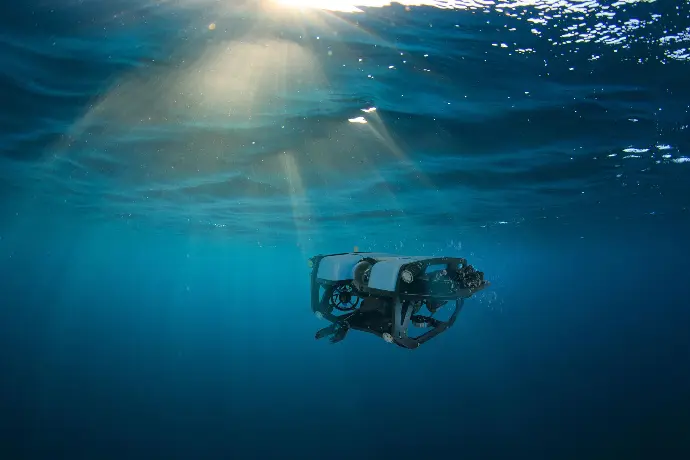
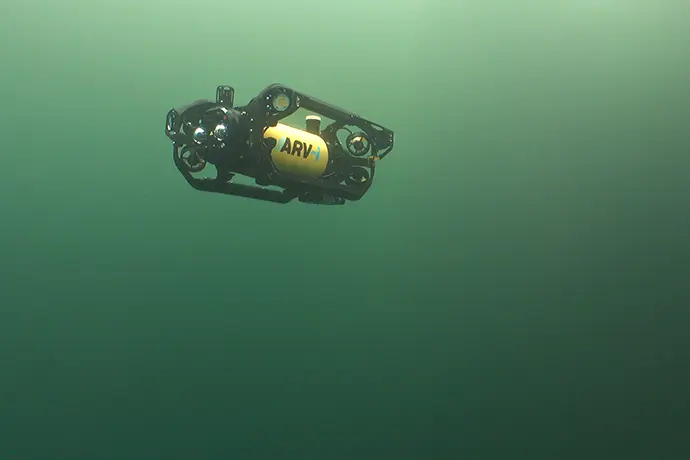
Precise maneuvers are necessary for safe and effective operations during underwater inspections. Integrating our DVLs with the vehicle control system can immediately improve the control, stability, and handling of your ROVs.
Enhanced vehicle control, stability, and station-keeping are critical for ROVs and AUVs in complex environments like offshore oil platforms, nuclear power plant cooling systems, deep-sea mining, and subsea cable inspections. These operations often occur in confined spaces, strong currents, or extreme depths, where precise navigation and maneuvers are required to avoid collisions and damage.
Tasks such as inspecting hydroelectric dams, ship hulls, underwater tunnels, and bridge foundations also demand stability in challenging conditions. Accurate control ensures safety and efficiency in these high-stakes, high-risk environments.
Precise tracking and absolute positioning
in challenging environments
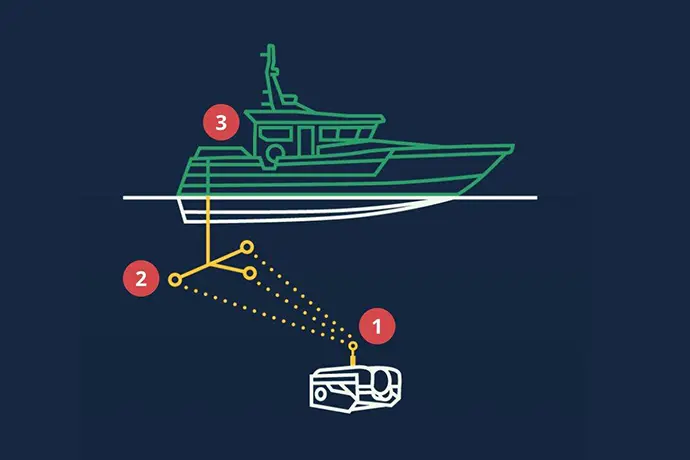
A good acoustic positioning system offers operators at the surface the ability to track their assets and they provide a means for vehicles operating autonomously below the surface to get an absolute position fix from the surface, where there is GNSS. This surface fix is useful for vehicles employing navigation solutions that accumulate errors over time or distance.
Precise tracking and positioning are essential for underwater inspections in challenging environments. It's critical for subsea cable inspections, ensuring accurate tracking along long stretches of subsea cables, and for offshore oil platforms, where navigating complex structures requires precise positioning to allow for accurate documentation of areas of interest or concern.
In confined spaces like underwater tunnels, bridge foundations, and (nuclear) power plant cooling systems, precise tracking is vital to perform detailed inspections safely and efficiently.
Our Underwater GPS (UGPS) is a Short Base Line (SBL) system that provides AUV operators with precise positioning, even in the most challenging environments such as shallow waters, tanks, pools, or around complex installations. With a focus on portability, efficiency, and ease of use, our UGPS ensures accurate positioning and tracking within 100 to 300 meters, simplifying underwater inspections.
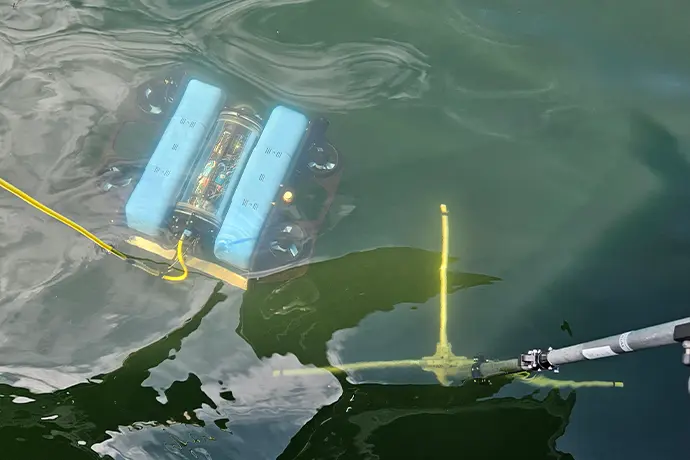
Inspect clearly, even with no visibility
Turbidity from sediment, particles, and organic matter in the water often reduces visibility, especially near the seabed or in shallow coastal areas. Murky or polluted waters, commonly found in industrial areas, harbors, and near runoff points, can also obscure visibility, while strong underwater currents may stir up sediment, worsening clarity. A great solution for this problem is the use of 3D sonar.
When you can’t see anything on the camera of your underwater vehicle, our real-time multibeam imaging sonar can provide you with clear 3D imaging of the object that you’re inspecting. The digitized point cloud data that our 3D sonar provides is ideal for detailed inspections and for creating intricate 3D point cloud models.
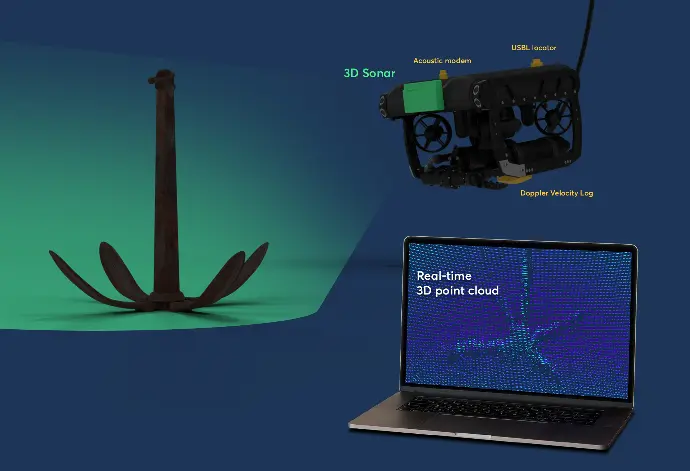
Our Sonar 3D-15 can for instance provide clear 3D images of pipelines, power cables, and their surrounding environments, enabling inspectors to identify potential damage. This is essential for early detection and maintenance and makes it easier to spot potential issues like sediment buildup or structural damage. With detailed 3D imaging, you can reveal issues with structural integrity and potential weaknesses during infrastructure inspections. This is vital for assessing the overall health of underwater structures.
Our Sonar 3D-15 is designed to fit any size of underwater vehicle, with its compact and efficient design and mere 0.4 kg in-water weight. For real time viewing you also don’t need to install software because the sonar's web-based Graphical User Interface (GUI) offers easy access, aligning with Water Linked's commitment to user-friendliness.
Communicate issues swiftly and reliably for smoother inspections
The Modem M16 from Water Linked can play an important role in enhancing underwater inspections by ensuring reliable communication between surface vessels and underwater vehicles like ROVs and AUVs.
With multiple modems integrated into the system, operators can send critical data from the surface to the underwater vehicle and also between vehicles, ensuring all systems are wirelessly communicating with one another. For example, during a pipeline inspection, real-time updates allow the AUV to alter its planned mission, allowing for last-minute changes to maximize operational efficiency.
Additionally, the Modem M16 enables the underwater vehicle to send status updates and alerts back to the surface, providing immediate feedback on the vehicle’s condition or environmental changes. In a power plant inspection, this capability could be critical for detecting any potential risks, such as structural damage or malfunction, allowing for quick surface intervention.
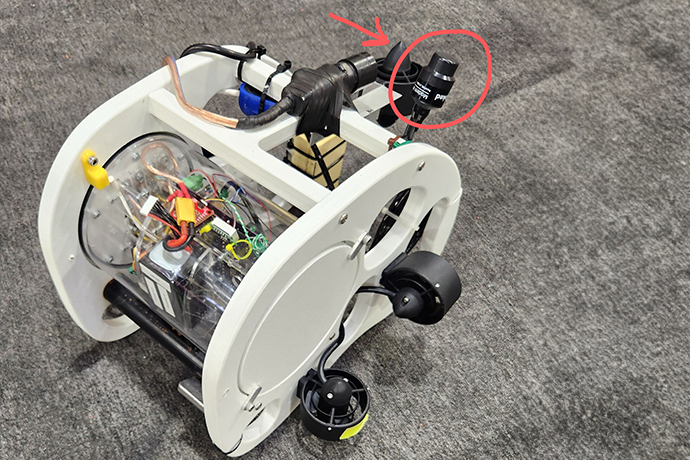
Photo courtesy: Desert WAVE team
Moreover, the Modem M16 supports inter-ROV and AUV coordination, which can be particularly valuable during complex missions, such as inspecting large-scale subsea infrastructure or managing emergency operations. Facilitating communication between multiple vehicles, ensures coordinated movements, improving the efficiency of inspections undertaken by more than one vehicle.
With its rapid boot-up time and low power consumption, the Modem M16 is ideal for long-duration missions, enabling AUVs to operate for extended periods without draining significant power. This is particularly useful in remote operations, where energy efficiency is vital.
Its capability to transmit and receive data with just two watt-seconds of power ensures that even during extended or critical missions, such as military or emergency operations, the AUV remains fully operational and ready to act at a moment’s notice. Through efficient communication and power management, the Modem M16 enhances the effectiveness and safety of underwater inspections.
Integrate your inspection ROVs or AUVs with our sensors to maximize inspection efficiency
Our navigation solutions fit any size ROV or AUV, providing a compact yet powerful suite of tools designed to meet the unique challenges of underwater navigation, inspection, and survey tasks. By integrating our DVL, UGPS, acoustic modem, and 3D sonar technologies with other sensors, you equip your ROV or AUV with the most advanced navigation system available, ensuring mission success in even the most demanding underwater conditions.
Explore our range of products today and elevate your AUV or ROV capabilities with our state-of-the-art navigation solutions.
Product Features
Small size
Our sensors are all developed to fit on small vehicles as well as bigger ones, without compromising performance.
Light weight
Lightweight sensors allow fitment on lighter vehicles, and leave you with excess payload capacity for other equipment.
Low power consumption
Our smart, proprietary technology leaves more power for your other devices or can help free up payload capacity due to requiring
smaller battery packs.
The DVL's output was fused with other sensor data to deliver even more precise navigation and altitude control, enhancing our AUVs' ability to carry out operations and navigate with great precision.
- Craig Anderson, co-founder, Boxfish
Product Options
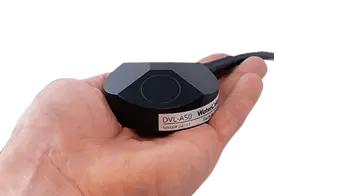

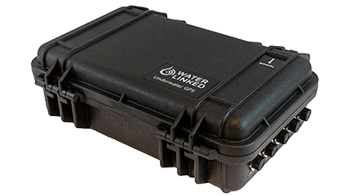
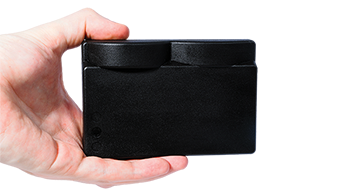
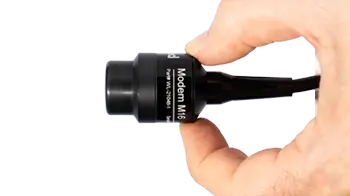
Customer stories